- +86-18632761626
- [email protected]
- Renqiu, Hebei Province, China
Mud Pump Accessories
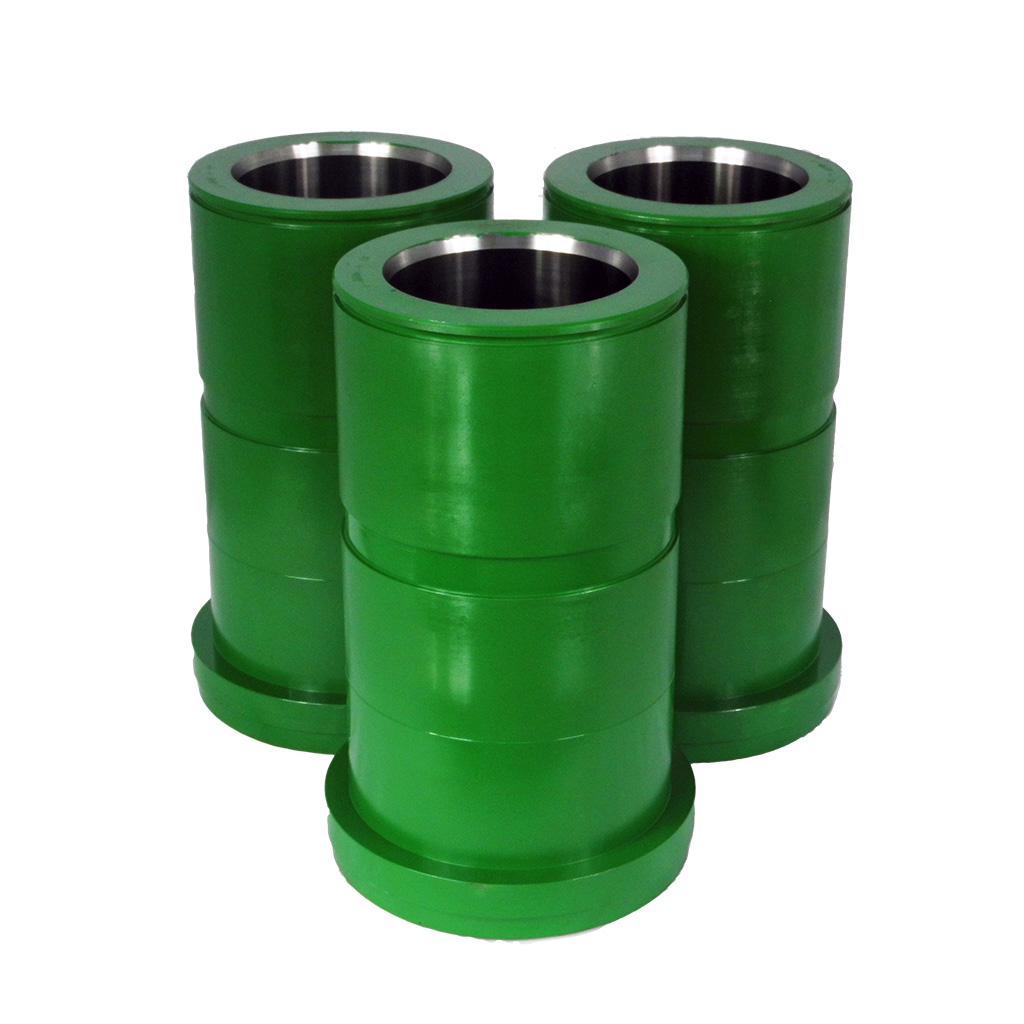
Bimetallic Cylinder Liner
The bimetallic cylinder liner, formed by the tight integration of two layers of material, offers exceptional performance. The outer layer is enhanced for wear resistance through forging processes, while the inner layer is made of high-chromium material for excellent wear and corrosion resistance. After precise heat treatment, its hardness can reach up to 62 on the Rockwell C scale. During the manufacturing process, we strictly control dimensions to ensure they fall within tolerance ranges, thereby simplifying the installation process. The inner layer has a high level of surface finish, superior wear resistance, and long-lasting corrosion resistance. This makes the cylinder liner highly suitable for a variety of harsh working environments and ensures its long lifespan.
Out Layer: 45#forged,
Tensile Strengthσb>610MPa,
Yield Strengthσs>450MPa,
Elongation§>17%,
Hardness HB180-200.
Inner Layer:High chromium cast iron (centrifugal casting)
Annealed Hardness: HRC≤40,
Quenching Hardness: HRC60 -67。
Chemical Components:C 2.8%-3.1% Cr 26%-28% Si 0.6%-0.9%
Mn 0.5%-1% Mo 0.5%-0.8% S , P <0.05%;
Hydraulic Cylinder
Mud Pump Cylinder Liners for W Series, 3NB Series, and PZ Series, with a monthly production capacity of over 50 pieces, have achieved specialization and standardization.
- The raw material is forged from high-strength alloy steel, either 35 CrMoA or 40Cr MoMn, and undergoes ultrasonic testing as per Class III forging standards. Secondary refining is done in an electric furnace or through deoxidation treatment. After normalization, the blanks are roughly machined and then undergo quenching and tempering, achieving an internal wall hardness of HB285-330.
- Forgings are executed from three directions with a forging ratio not less than 4.0:1.0. During the forging process, there are no defects such as laminations, cracks, impurities, oversize, or overburning. There is no welding involved, and the forgings fully comply with JB/TQ252-81 regulations and are inspected as Class III forgings.
- The intersecting lines of the internal cylindrical surfaces are manually or wheel-ground to form a rounded edge with a radius of R≥8. Hydrostatic testing is performed at 53Mpa, with a hold time of one hour.
- Ultrasonic testing, magnetic particle inspection, dimensional inspection, and heat treatment inspection are conducted.
- Mechanical properties are as follows: σb≥850Mpa, σS≥670Mpa, elongation σ≥5%, and reduction in area ψ≥30%.
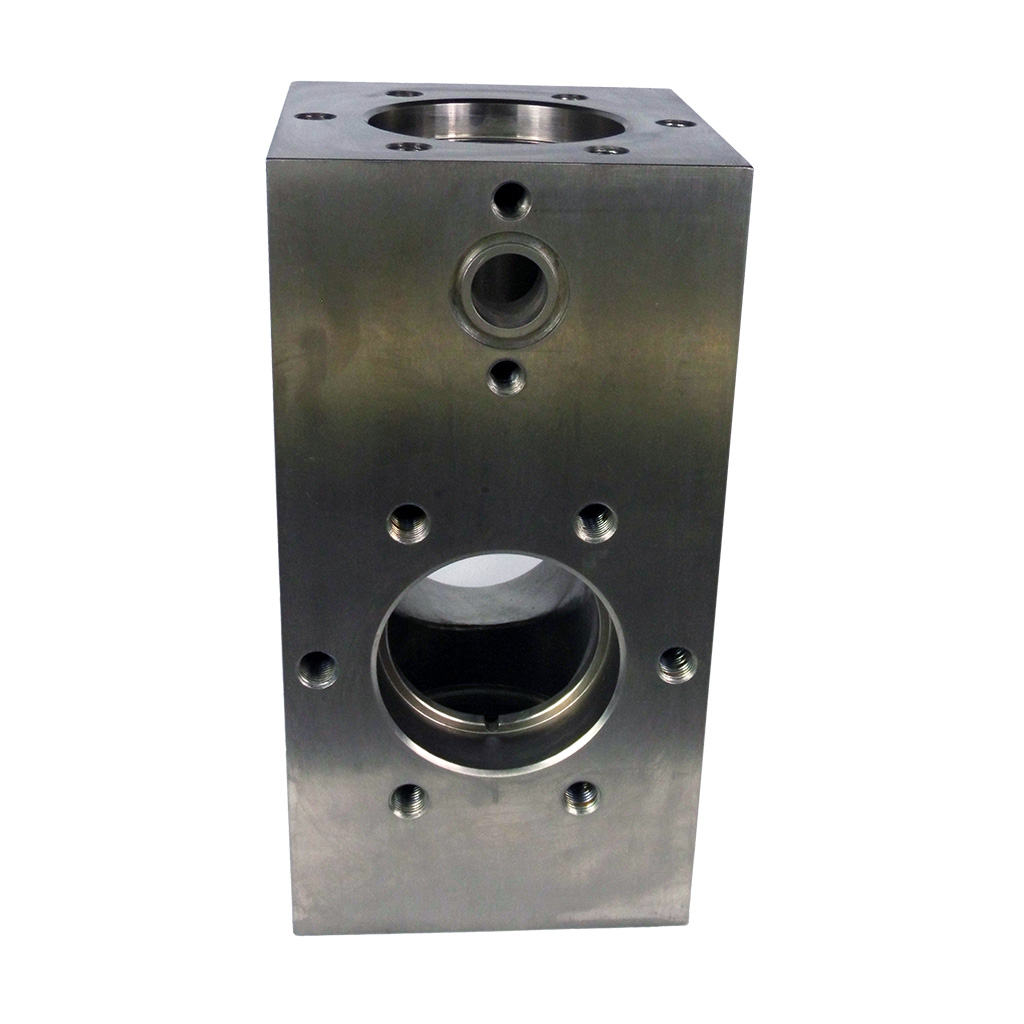
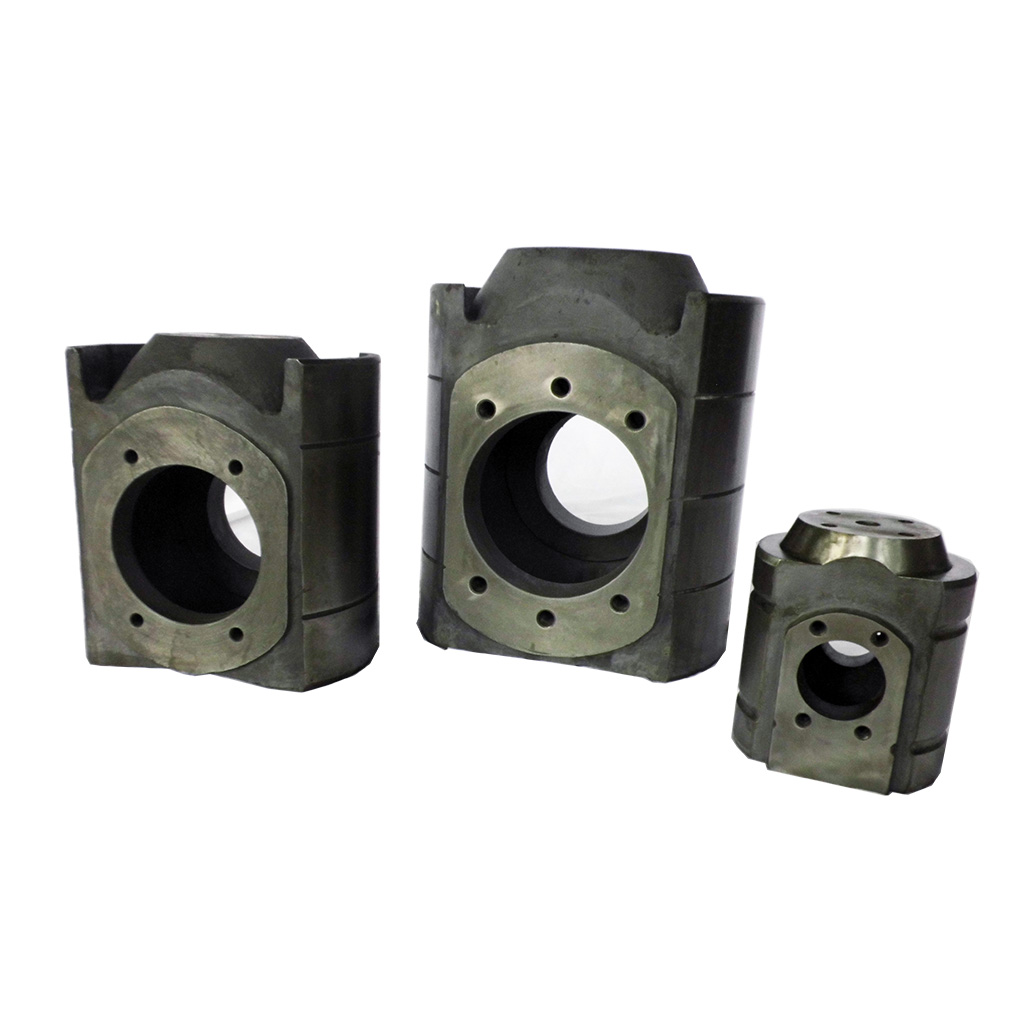
Cross Head
The crosshead is made of ductile iron through integral casting, offering good wear resistance.